Level Up Your Management Skills with Six Sigma
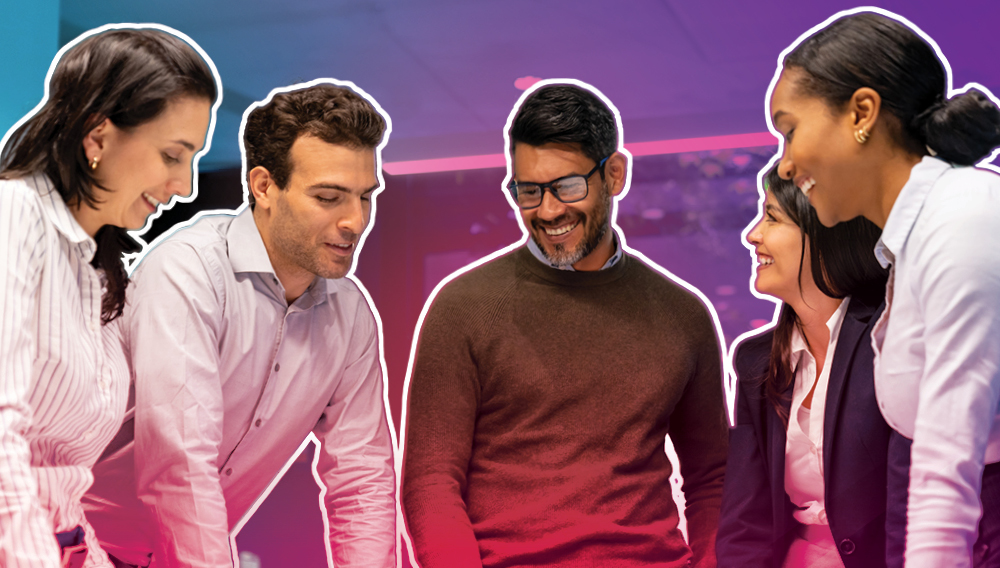
What do Intel, PepsiCo, and Volvo have in common? They all have a not-so-secret weapon helping them manage production and keep customers happy: Six Sigma, a data-driven methodology used to improve systems and reduce defects.
From computer processors to beverage manufacturing, organizations are constantly striving for the smallest margins of error in their processes to meet high levels of competition and satisfy customers accustomed to consistent products delivered fast. Six Sigma is not only relied on by some of the world’s biggest manufacturers but also a philosophy of continuous improvement and customer satisfaction you can use to dramatically enhance your management skills, no matter your industry.
What Is Six Sigma?
Six Sigma can get complicated quickly, but at its core, it is a method for applying statistical analysis to manufacturing processes to remove variation and eliminate error. It operates on the idea that by turning work into data, we can track, measure, and ultimately control the output.
The techniques and tools that form the method were developed in the 1980s by Motorola engineer Bill Smith as a proposal to improve the quality of the company’s products. The system gained even greater prominence in the 1990s when Jack Welch, then CEO of General Electric, championed Six Sigma as one of the key tools he used to overhaul business operations and achieve record growth for the company.
Why Is It Called Six Sigma?
The name “Six Sigma” comes from the bell curve in statistics, where one sigma represents one standard deviation from the mean. When a process reaches six sigma, that means there are only 3.4 defects per million opportunities. The method was developed for large-scale manufacturing processes, and it’s in those industries where you’ll find it most used, but the principles can also be applied to find continuous improvement and efficiency in other areas of an organization’s processes, to identify trends, to predict outcomes, and to make informed decisions that drive positive change.
How Is Lean Six Sigma Different?
Six Sigma seeks to minimize errors and inconsistencies during production, whereas Lean Six Sigma looks to streamline or “lean out” processes throughout an entire workflow. The traditional method defines waste as defective products and uses statistical analysis to drive improvements. In Lean Six Sigma, waste is defined more broadly as any activity that doesn’t benefit the customer and can include wasted time, effort, or materials. The tools for improvement in Lean rely less on numerical data and more on process visualizations like flow charts and value maps.
What Are the Steps of Six Sigma?
Six Sigma relies on a structured approach to process improvement involving two sets of five key phases that practitioners refer to by their initialisms, DMAIC and DMADV. Which set you use depends on what type of process you’re trying to impact.
DMAIC
Geared toward existing processes, DMAIC stands for “define,” “measure,” “analyze,” “improve,” and “control.” Each phase is designed to produce data that is actionable in the next step.
Define
Identify the problem and process to be improved. Then, create project goals, a project charter, a process map, and the metrics by which you’ll measure success.
Measure
Gather data and measure key performance indicators related to the process.
Analyze
Examine the data to identify the root causes of the problem. Use process data for hypothesis testing, visualization, and validation.
Improve
Generate a solution and create new process maps for improvements. Implement a pilot program, continue measurements, and adjust as needed.
Control
Monitor the improved process to ensure that continuous improvement is sustained over time. Document and standardize changes and then launch a plan of training and communication on new processes for stakeholders across the organization.
DMADV
DMADV shares its first three steps with DMAIC, but they are applied slightly differently. The last two steps, “design” and “verify,” are specifically tailored to creating new processes.
Define
Identify the customer’s needs, goals, and success metrics of the new product.
Measure
Establish parameters for the product and process that are measurable, allowing data to be collected and compared with the specified requirements.
Analyze
Study the proposed specifications, making changes if necessary, to proactively limit future issues and errors.
Design
Using information gathered during analysis, design the complete process and create prototypes.
Verify
Ensure that the final product meets the customer’s requirements and that the process design is viable, sustainable, and error-free under real-world conditions.
DMAIC vs. DMADV
DMAIC is used to improve a process that already exists but is producing an unacceptable number of errors. For example, say you oversee a factory that produces cars, but customers complain that the side mirrors keep falling off. DMAIC can help pinpoint where in the production line the mirrors become faulty, why the fault is occurring, and then what changes need to be made in the process to correct it.
DMADV is used to create completely new processes that meet the customer’s needs and specifications. Now, imagine that your car factory got the order to pivot production and manufacture toasters instead. The steps of DMADV address the process of designing, testing, and implementing the new systems needed to make the switch.
Where Can You Learn About Six Sigma?
If you’re interested in learning more about Six Sigma, there are an abundance of training and certification programs offered online and in person. Certification levels are named after colored belts, much like martial arts, and go from a white belt, where you learn the fundamentals, to a master black belt that designates you have the experience needed to implement Six Sigma projects at an enterprise level and coach others in the method across teams.
By incorporating these principles and methodologies into their management style, leaders can become more effective, efficient, and confident in their decision-making and overall leadership. But Six Sigma is only a tool, and it’s at its most impactful when wielded by those with the comprehensive business education to know how and where to use it. Excelsior offers a bachelor’s degree in business as well as an online MBA program and a hybrid Executive MBA program designed to give you a foundation of analytical skills and leadership ability that complements Sig Sigma training and earns you a seat at the table when important decisions are being made.